If you have owned a building for a decade or two you will remember the days when you used to see your elevator mechanic monthly or more. Your building engineers were friends with him and whenever there was a problem he was there that same day. Unfortunately, times have changed and in a lot of cities this is no longer the case.
I won’t get into the history now of why that has changed, but how much elevator service should you expect from your maintenance provider? Well, you probably signed a contract that does not specify how many visits or hours of preventive maintenance needs to be performed, but instead alludes to systematic and routine maintenance. Vague right? Well that is on purpose. Perhaps when you signed your contract your sales rep told you a certain amount of visits. That sales rep is probably long gone.
Expectations for your elevator preventative maintenance
- 4 maintenance visits per year for hydraulic elevators.
- 12 maintenance visits per year for traction elevators.
Are these amount of visits designed to extend the longevity of your equipment as some elevator service companies promise? Well, it depends. If you have a brand new hydraulic elevator there is not much to do. Your mechanic should check the operation of the doors, make sure all the lights are working, and do some basic cleaning. In this case, 4 visits are year are probably satisfactory.
Now if you have a traction elevator that is 30+ years old you probably need at least 12 visits a year if not more, or consider an elevator modernization. Depending on the number of stops of your elevator, your technician could easily spend a whole day performing maintenance. But, here is the problem.
The major elevator companies determine how many elevators each mechanic can have on his route based upon hydraulic versus traction elevators. Not, based on average age. That means you are probably not getting the appropriate amount of service, but legally your elevator company is meeting the terms of your agreement.
Your elevator service company is not honoring their contact
In my career I have seen plenty of times that contracts were not honored because of lack of maintenance visits. So what should you do if you feel this is the case?
Immediately ask your elevator service company for your records for the past 2-3 years. Legally, according to ASME A17.1-2013, they must keep a maintenance record in your machine room. Take a look and see if they have been keeping up their end of the bargain. You might see visits to your building that you do not recall. Can those records be manipulated? Unfortunately, yes they can.
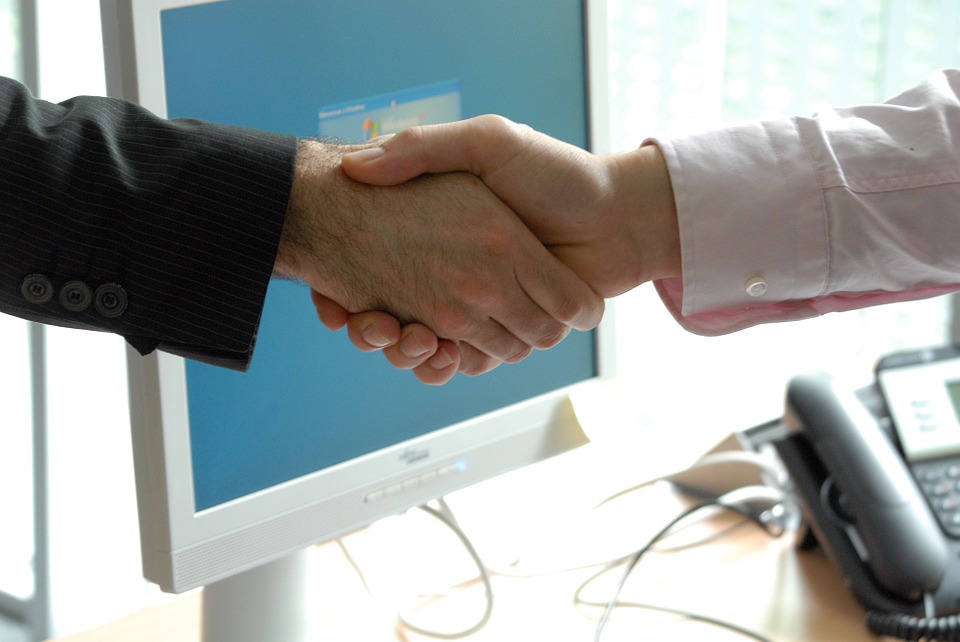
Elevator mechanics typically will have a PDA, tablet or phone that they record their visits in that are verified by GPS. Some mechanics (in my experience this was extremely rare), may do “drive-bys”. This means they are next to your building and mark a visit, so it shows up in the records. If you can prove this is the case (camera footage, the building was closed that day, etc.), you should bring this to the attention of your account manager or service manager. This may be a disciplinary situation.
More than likely though, your mechanic is stretched thin with too many units on his route. You should ask for a partial refund on your contract. Your elevator service provider will put up a hell of a fight, but legally they do owe you money. They likely won’t give you a full refund because they will say the contract still covered your insurance, callbacks and annual testing. This is true, but if you really put up a fight they might refund you the full amount.
If you are stuck in a long term contract this may be a way out if you are very unsatisfied with your service. They broke their contract by not fulfilling “systematic and periodic maintenance” which should allow you to end your relationship. Unless you are very unsatisfied I don’t necessarily recommend terminating your relationship without giving them a second chance. Your mechanic likely has historic knowledge of your elevator that is invaluable.
Be the squeaky wheel
You may face another situation which is much more common. Your mechanic shows up the required amount of times but is only there for half an hour before he rushes off for another call. Some mechanics will ride the elevator and your elevator company will say that is their preventative maintenance for the month! Here is where it gets tricky and frustrating. Legally, they could claim they have satisfied their contractual requirements. But they are not really honoring the spirit of the contract. In essence, they are not extending the life of the elevator with preventative maintenance.
If this is the case, you or your building engineer will likely have to be the squeaky wheel. Your elevator service provider is terrified of losing customers. Send an email to your account manager or service manager asking that from now on your mechanic must sign in and out of a log book, and let you or someone on your staff know what he did. This will be a frustrating process as in my experience after the first visit or two the process breaks down and the mechanic stops checking in. If your provider still can’t meet these expectations it may be time to look for another service provider, or hire an elevator consultant.